Removal of Cr(VI) from aqueous solution using ball mill …
This study used ball-milling modified wheat biochar (BM-WB) as an adsorption material to explore the optimal operating parameters of BM-WB adsorption of Cr(VI) and the dynamic mechanism of the ...
اقرأ أكثر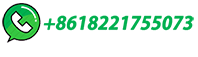
Three rules for the optimum ball mill setup
OPTIMUM BALL MILL SETUP The success of a ball milling application depends on the correct selection of accessories and process parameters. This includes jar sizes, jar materials, ball sizes, number of balls, particle size, material fill level, speed and time or cycle programs. Finding the optimum setup is a challenging task because the result ...
اقرأ أكثر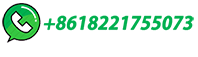
AMIT 135: Lesson 7 Ball Mills & Circuits – Mining …
Assist the lift of the media and ore to the desired height in the mill. Liners can be made of manganese steel, Ni hard or high carbon steel and hard rubber or synthetic material that is 65 – 75 mm thick. The liners can be: …
اقرأ أكثر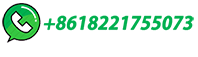
Effect of ball and feed particle size distribution on the milling
The same policy is employed for the make-up charge where adding different ball sizes is done in order to optimize the mill performance. Chimwani et al. (2015) developed a simulation program that could predict optimal make-up balls to be added in order to achieve a required product fineness.
اقرأ أكثر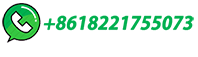
Three rules for the optimum ball mill setup
THREE RULES FOR THE OPTIMUM BALL MILL SETUP. The success of a ball milling application depends on the correct selection of accessories and process parameters. …
اقرأ أكثر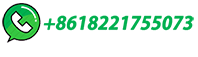
DEM Investigation of Mill Speed and Lifter Face Angle on Charge …
For dry tests, the orthogonal analysis indicates that the influence order of four factors on power-mass ratio is ball filling, mill speed, powder-grinding media ratio and lifter profile and the ...
اقرأ أكثر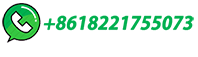
Optimization of continuous ball mills used for finish …
The L/D ratio of the ball mill was varied in four steps of 1.75, 2.1, 2.79 and 3.49, and the ball charge filling ratio was varied in three steps of 15%, 20% and 25%. The experiments clearly indicated that the optimal L/D ratio and the optimal ball charge filling ratio are different for each feed fineness.
اقرأ أكثر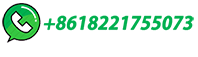
Ball Mill Linings
Ball mill liner components: Our ball mill liners solutions can be fitted with MultoMet composite lifter bars, shell plates and head plates. The MultoMet range utilises Hardox 500 wear-resistant steel attached to the leading edges of the lifter bar array and embedded within shell plates and head plates, ensuring maximum abrasion and impact resistance.
اقرأ أكثر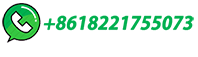
Exploring Ball Mill Diagram: A Comprehensive Guide
The speed of ball mill rotation is a critical parameter which determines the grinding efficiency and the end product quality. The optimum speed will differ depending on the mill's diameter, the size and density of the grinding media, and …
اقرأ أكثر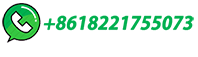
Factors Affecting Ball Mill Grinding Efficiency
The following are factors that have been investigated and applied in conventional ball milling in order to maximize grinding efficiency: a) Mill Geometry and Speed – Bond (1954) observed grinding efficiency to be a function of ball mill diameter, and established empirical relationships for recommended media size and mill speed …
اقرأ أكثر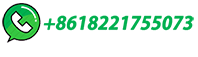
Ball Mills
Manganese liners for Ball-Rod Mills are the world famous AMSCO Brand, and are the best obtainable. The first cost is the highest, but in most cases the cost per ton of ore ground is the lowest. ... gears, steel liners and optional grinding media charge/load. Ball Mills or Rod Mills in a complete range of sizes up to 10′ diameter x 20′ long ...
اقرأ أكثر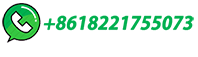
THE OPTIMAL BALL DIAMETER IN A MILL
where d* is the filling load of grains less than d, d is the grain diameter, dmax is the maximum grain diameter, m is the exponent which characterizes the grain size …
اقرأ أكثر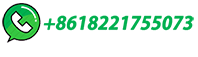
BALL MILLS Ball mill optimisation
The importance of second chamber optimisation. It is also important to evaluate the grinding efficiency and ball charge efficiency for a. amber grinding process evaluationof ball …
اقرأ أكثر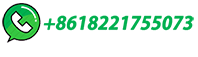
Research on an Accurate Simulation Modeling and Charge …
An elaborate description of the charge movement inside the ball mill is essential. This study focuses on a laboratory-scale ball mill and utilizes a discrete …
اقرأ أكثر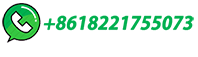
The Effect of Ball Size Diameter on Milling Performance
the other mills, as previously mentioned ball mills have a very low efficiency in terms of utilizing the energy generated towards particle size reduction. The diameter of the balls used in ball mills play a significant role in the improvement and optimization of the efficiency of the mill [4]. The optimum rotation speed of a mill, which is the ...
اقرأ أكثر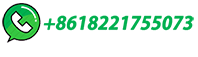
Effect of grinding media on the milling efficiency of a ball mill
Various operational parameters, such as mill speed, the ball charge composition, charge filling, lifter type, and lifter number, significantly impact ball milling grinding efficiency [3]. The ...
اقرأ أكثر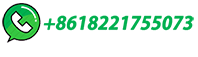
Ball Mill Liner Design
There are many different designs and styles of ball mill liners. As with grinding balls local economics and ultimately operating costs determine the best design and material to use. The initial set of liners is rarely the final design selected. Based upon individual experience, mill superintendents develop preferences for liner designs. The …
اقرأ أكثر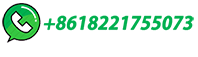
how to calculate ball charge in sag mills
how to calculate sag mill ball charge – Gulin Mining Gulin Services, LLC. mill charge and speed. SAG Mill product…
اقرأ أكثر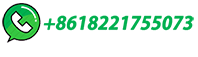
How to calculate the balls needed in a ball mill?
To calculate the balls needed in a ball mill, you need to know the capacity of the mill and the desired grind size. You can then use the following equation to calculate the number of balls needed ...
اقرأ أكثر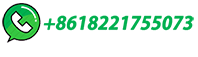
babcock e type ball mill – Grinding Mill China
CemServConsult . BABCOCK vertical coal mills.Produktbilder/ Pictures: … 2 Babcock vertical coal mills, type 8.5 E 9 (ring ball mill), with separator, hydraulic system, … » Free online chat! PS-410 – E and EL Pulverizer Modifications for Optimum Performance If the E-type mill includes a yoke-driven rotating … package limits ball and …
اقرأ أكثر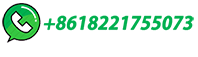
Determining Optimum Wet Milling and Leaching …
More tests were done according to the conditions specified in Table 1 using the ball size, media and charge filling shown in Table 2. The measured feed material (-1700+850 μm), media and water were loaded into the mill and milled for 3 minutes. The mill was stopped and its contents emptied and stored in a bucket.
اقرأ أكثر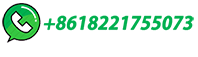
Ball Milling Guide
Charge – This is the contents of the milling jar, ... measured by volume. So for example, a 6 litre mill jar will have 3 litres of milling media and 1.5 litres of material to be milled. Speed. ... they will mill slower. Particle size. Ball milling has been used to grind materials to average particle sizes of 20 nanometres and finer, with ...
اقرأ أكثر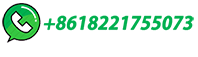
Mill Steel Charge Volume Calculation
We can calculate the steel charge volume of a ball or rod mill and express it as the % of the volume within the liners that is filled with grinding media.
اقرأ أكثر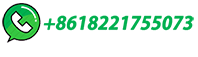
Guidelines for sample amount and ball charge Content
In addition to the instrument settings and the ball size, the filling level of ... Ball charge Mixer Mills MM 200 / MM 400 / MM 500 vario / CryoMill The MM 400 and the CryoMill (at room temperature) are suitable for wet grinding. For optimal wet grinding results, the MM 500 nano or Planetary Ball Mills should be used (optimized jar geometry).
اقرأ أكثر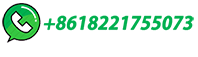
How Ball Mills Lifter Bar Affects Charge Motion
For a given rotating speed and filling of the mill, impact velocities of balls and the nature of forces developed inside the mill can be controlled by the most favorable configuration of lifter bars. ... There are …
اقرأ أكثر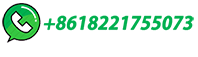
Research on an Accurate Simulation Modeling and Charge …
A ball mill is a type of complex grinding device. Having knowledge of its charge-load behavior is key to determining the operating conditions that provide the optimum mill throughput. An elaborate description of the charge movement inside the ball mill is essential. This study focuses on a laboratory-scale ball mill and utilizes a …
اقرأ أكثر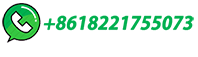
The optimal ball diameter in a mill | Request PDF
This paper covers theoretical and experimental explorations for the sake of determining the optimal ball charge in mills. In the first part of the paper, on the basis of the theoretical analysis ...
اقرأ أكثر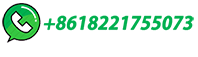
Ball charge optimization
Previous Post Next Post Contents1 Ball charge optimization2 1 How to use the BP2.1 2 Description of the main indicators used in this BP2.1.0.1 The residue on 2mm/4mm before partition wall2.1.0.2 Material filling level and ball charge expansion2.1.1 Cement mill specific power 1st compartment 2.1.2 Raw mill specific power 1st compartment Ball …
اقرأ أكثر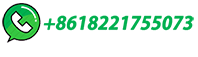
Calculate Ball Mill Grinding Capacity
A) Total Apparent Volumetric Charge Filling – including balls and excess slurry on top of the ball charge, plus the interstitial voids in between the balls – expressed as a percentage of the net internal mill …
اقرأ أكثر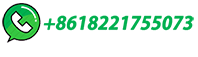
Factors Affecting Ball Mill Grinding Efficiency
The following are factors that have been investigated and applied in conventional ball milling in order to maximize grinding efficiency: a) Mill Geometry and Speed – Bond (1954) observed grinding efficiency …
اقرأ أكثر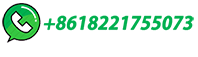