Update on electric cement kilns
How this would fit with any kiln electrification plans is unknown. However, one attraction of moving to an electrical kiln, for all of the projects above, is to cut out the 40 – 50% of a cement plant's CO 2 emissions that arise from the fuel that is burnt. Taking a kiln electric also makes CO 2 capture easier.
اقرأ أكثر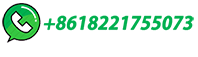
cement production
This course provides a comprehensive overview of the cement production process, from raw material selection to the final product. You'll learn about the different types of cement, the different stages of production, and the various production processes, including kiln technology, grinding and milling, and material handling.
اقرأ أكثر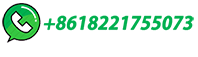
Cement Kiln
A cement kiln is a kind of construction material manufacturing equipment, mainly used in the production of Portland cement and other types of hydraulic cement. As the main cement equipment, it is an integral part …
اقرأ أكثر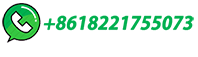
Kiln predictive modelization for performance optimization
The process of cement manufacturing is both energy intensive and difficult to control. This complicated process results in inefficiencies in energy consumption and variations in cement quality with many complex influencing process factors such as input raw materials, variable fuels, firing conditions including temperature, burning, and reside …
اقرأ أكثر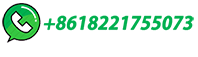
Portland Cement Manufacturing Industry: National Emission Standards …
Portland cement manufacturing is an energy intensive process in which cement is made by grinding and heating a mixture of raw materials such as limestone, clay, sand, and iron ore in a rotary kiln. The kiln is a large furnace that is fueled by coal, oil, gas, coke and/or various waste materials.
اقرأ أكثر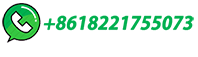
The Cement Manufacturing Process
How cement is made. Cement manufacturing is a complex process that begins with mining and then grinding raw materials that include limestone and clay, to a fine powder, called raw meal, which …
اقرأ أكثر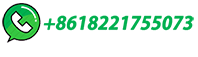
Final Revisions to AP-42 Chapter 11, Section 6
1 30500623 - Industrial Processes; Mineral Products; Cement Manufacturing (Dry Process); Preheater/Precalciner Kiln **Value represents new quality ratings given to factors based on Emissions Factors Procedures Document. Factors are given quality ratings based on representativeness of factor (i.e. Moderately = Moderately representative of the …
اقرأ أكثر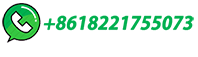
The Cement Manufacturing Process
Cement manufacturing is a complex process that begins with mining and then grinding raw materials that include limestone and clay, to a fine powder, called raw meal, which is then heated to a sintering …
اقرأ أكثر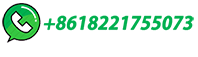
Chapter 4 Cement Manufacturing and Process Control
The cement is now ready for use in construction projects. The flow sheet of cement manufacturing is given in Fig. 4.1. Kiln feed is subjected to succes-sive physical and chemical reactions as its temperature rises gradually as shown in Table 4.1. 4.2 Raw Material The major raw materials used as a source of CaO for cement manufacturing are
اقرأ أكثر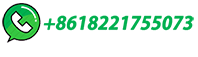
Cement Kiln
The rotary cement kiln is the heart of the cement-manufacturing process. The raw materials which are the basis of cement are blended in a finally ground feed which is continually introduced into the rotary kiln. The raw materials are so proportioned that the correct balance of chemical constituents is present in the feed.
اقرأ أكثر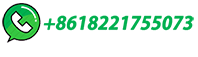
Cement Manufacturing and Process Control | SpringerLink
Manufacturing process of Portland cement clinker is discussed, which is relevant to a Refractory technologist engaged in manufacturing or development of refractories for cement industry. ... In the cement kiln, all the ingredients are heated to about 1400–1500 °C in huge horizontal cylindrical steel tubular vessel called rotary kiln, …
اقرأ أكثر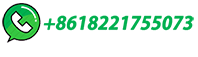
A comprehensive review on Advanced Process Control of cement kiln
Pyro processing plays a significant role in the cement manufacturing process. A Rotary kiln is considered the heart of pyro-processing and is responsible for cement quality. As shown in Fig. 5, the kiln is made of a hollow steel cylinder coated with firebricks to minimise heat loss and inclined at a slope of (1–4°) to allow for smooth ...
اقرأ أكثر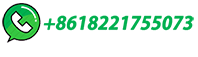
Types of Rotary Kilns
Such a kiln usually requires additional labor to attend the granulator plant. DRY-PROCESS KILNS. As the term indicates, in this process the kiln feed enters the kiln in dry powder form. Dry-process kiln dimensions are similar to wet kilns in that they are long and typically show a length-to-diameter ratio of approxi mately 30:1 to 35:1.
اقرأ أكثر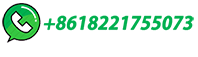
Rotary Kilns
Worn Rotary Kiln Refractory. Batch Rotary Kiln Testing. Kiln Alignment Software. Processing Challenges When Working with Rotary Kilns. FEECO Batch Kiln Brochure. Industry Focus COVID-19 Demands Medical …
اقرأ أكثر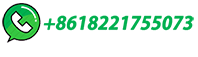
Cement manufacturing: components of a cement …
This page and the linked pages below summarize the cement manufacturing process from the perspective of the individual components of a cement plant - the kiln, the cement mill etc.. For information on …
اقرأ أكثر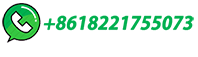
Cement Manufacturing Process- Wet and Dry Processes
Cement manufacturing is an intricate process involving the extraction and grinding of raw materials, followed by blending and heating in a kiln to produce clinker. This clinker is then ground with gypsum to create cement, a vital component for construction.
اقرأ أكثر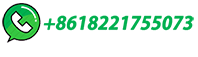
Explain manufacturing of Portland cement with labeled …
MANUFACTURING OF PORTLAND CEMENT : Raw materials of Portland cement is, (i) Calcareous Materials: It is lime stone. ... The kiln is supported on the columns of masonry or concrete and rested on roller bearing in slightly inclined position at the gradient of 1 in 25 to 1 in 30. The raw mix of dry process of corrected slurry of wet process is ...
اقرأ أكثر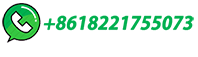
Wet Process Of Cement Manufacturing With Flow Chart
The following are the major disadvantages of the wet process of cement manufacturing, Mixing of Raw materials in wash mill with 35 to 50% water. Materials exiting the mill are called "slurry" and have flowability characteristics. The size of kiln needed for the manufacturing of cement is bigger.
اقرأ أكثر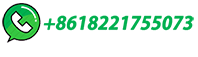
A Comprehensive Guide to the Cement Manufacturing …
Cement manufacturing is an industry that involves several steps, including the gathering of raw materials. ... Clinker is the principal component of cement. The kiln reactions from the following compounds: Tricalcium silicate (C₃S): this compound gives strength to the cement and hardening properties.
اقرأ أكثر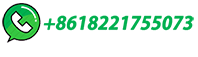
Cement Clinker Manufacturing Process with Reactions
Kiln phase. Since clinker is a complex mixture of ingredients, it requires a multi-staged heat treatment, which is done in the kiln. The main part of the manufacturing process of clinker takes place in the kiln. The stages in the kiln phase are as follows:
اقرأ أكثر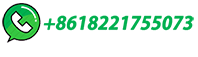
A Comprehensive Guide to the Cement Manufacturing Process
Cement manufacturing is an industry that involves several steps, including the gathering of raw materials. ... The raw material is preheated in a high structure …
اقرأ أكثر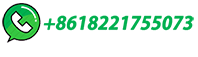
Environmental impacts and decarbonization strategies in the cement …
Zemba, S. et al. Emissions of metals and polychlorinated dibenzo(p)dioxins and furans (PCDD/Fs) from Portland cement manufacturing plants: Inter-kiln variability and dependence on fuel-types.
اقرأ أكثر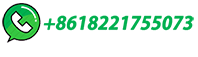
How Cement is Made
The kiln phase is the principal stage of the cement production process. Here, clinker is produced from the raw mix through a series of chemical reactions between calcium and …
اقرأ أكثر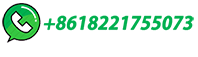
Process technology for efficient and sustainable cement production
As a pre-stage, ECRA is currently preparing a concept study for an oxyfuel pilot cement kiln [41]. Moreover, one cement producer is planning a pilot-scale test at its plant in France [42]. Due to the challenges involved with integration and the influences on the process and the material, a commercial application is not expected before 2030.
اقرأ أكثر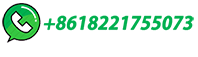
Recycling of Cement Kiln Dust as a Raw Material for Cement
Cement kiln dust (CKD) is a major by-product of cement manufacturing and has the potential to be recycled as a raw material if the high concentrations of chlorine and potassium are removed. This study tested four leaching solutions (distilled water and three organic acids) and determined the optimum reaction conditions. At a liquid/solid …
اقرأ أكثر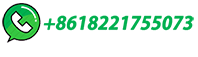
Modernizing cement manufacturing in China leads to …
NSP rotary kilns started to account for more than 10% of the market share in 2001, and China's national cement production peaked in 2014. Therefore, 2001 and 2014 are selected as typical years ...
اقرأ أكثر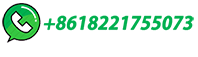
Kiln Control and Operation
The aim of clinker manufacturing is to produce a clinker that is neither overburned nor underburned, since both extremes are detrimental for the cement strength. The quality, most frequently expressed as free lime content or the liter weight, should vary only in a small range. ... Cement Kiln Firing Systems.
اقرأ أكثر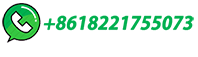
Petroleum Coke in the Cement Industry
cement kiln which operates at 1500°C melting the rock to produce clinker. This clinker is then further ground to a fine cement powder. ... Analysis of Sewage Sludge as Secondary Fuel for Cement Manufacturing," CHEMIICAL ENGIINEERIING TRANSACTIONS: A publication of The Italian Association of Chemical Engineering, vol. 29, pp. 457-462, …
اقرأ أكثر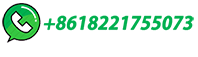
Manufacturing of Portland Cement – Process and Materials
The manufacture of Portland cement is a complex process and done in the following steps: grinding the raw materials, mixing them in certain proportions depending upon their purity and composition, and burning them to sintering in a kiln at a temperature of about 1350 to 1500 ⁰C. During this process, these materials partially fuse to form …
اقرأ أكثر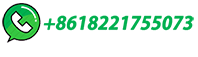